溶射加工について
溶射とは
溶射とは、皮膜を形成するコーティング技術の一種です。
燃焼ガスやプラズマ等を熱源として、材料を加熱し融し、これを、ガスまたは、圧縮エアーにより母材表面に吹き付けるという技術のことを溶射と呼びます。
燃焼ガスやプラズマ等を熱源として、コーティング材料を、加熱により溶融もしくは軟化させ、微粒子状にします。それをガスまたは、圧縮エアーにより加速し被覆対象物表面に衝突させて、扁平に潰れた粒子を凝固・堆積させます。
溶射を行うことで、耐久性の向上、寿命の向上、性能の向上など多くのメリットを付与します。
各種産業機械やシステムは、極めて苛酷な環境や条件にも耐えうるように設計する必要があります。その意味で“溶射”は製品性能に欠くことのできない表面改質技術です。
溶射技術は、防せい・防食に対する鉄鋼構造物などの基材保護及び化学機器装置などの耐薬品に対する環境遮断を目的とした溶射と、各工業分野の設備、装置などにおける耐摩耗、耐熱遮熱、絶縁などを目的とする機能的な溶射に区分されます。
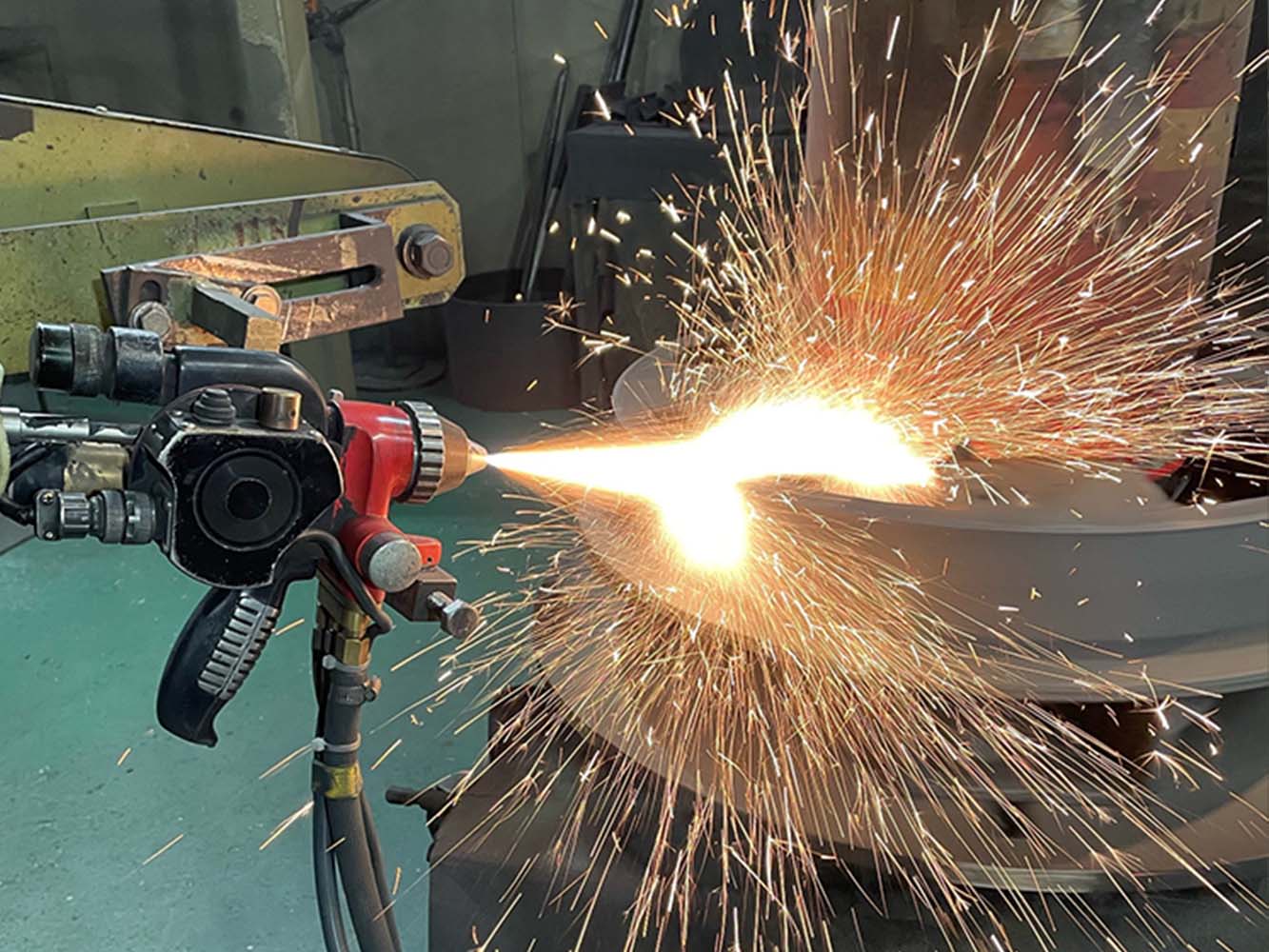
溶射の特徴
-
耐摩耗性の向上
「摩耗を防ぎたい」「摩耗してかなりすり減っている」そんな場合に溶射をおすすめします。
磨耗にあった溶射材の選定とお客様のコストメリットが最大限に引き出せる様ご提案させていただいております。
すり減った箇所に肉盛りをして、耐摩耗性を高めることも可能です。 -
防食・防腐食
溶射加工を行うことで、錆や腐食から守ることが可能です。 「材料が腐食してしまう」「製品が錆びる」 そんなことでお困りの場合は、溶射加工が最適です。
-
耐熱・遮熱
一部分だけ耐熱金属や遮熱材料で保護したい。又は溶けた金属内で金属製品を使用したい時には溶射が便利です!
-
遠赤外線・絶縁通電
非磁性な物に磁性合金を溶射して電磁調理器にかかる様にしたり、絶縁素材や通電素材を表面に処理する事によって電気の流れを変える事が出来ます。
溶射手法
-
ガス溶射
ガス溶射は1本の線状やロッド状のワイヤーを、酸素:燃焼炎により溶射材を溶解し、圧縮空気により微粒化した溶射材を母材表面に吹付ける溶射法です。
特徴
- 設備が簡易的な為現地工事に適しており動かせない素材への溶射が可能。
- アークに比べて表面粗度が細かく、高硬度な皮膜が形成される。
- 低温溶射の為被溶射材が変質・変化せず施工可能。
- アークに比べてクロム、カーボンの損失が少ない皮膜が形成される。
- 熱交換器や橋、鉄橋等の鉄鋼建設物の長期防食に大いに利用されている。
-
アーク溶射
アーク溶射法は、2本のワイヤーに電圧をかけてアークを発生させ、そのエネルギーで、ワイヤーを溶解し圧縮空気で微粒子化し、素材面に吹付け皮膜を形成します。
特徴
- 2本の異種金属、合金線を利用し疑似合金皮膜が形成出来る。
- 線材金属であれば、全て溶射可能。
- 低温溶射の為被溶射材が変質・変化せず施工可能。
- 形成皮膜がポーラス状である為気孔に油保有性に優れ摺動摩耗性が向上される。
- 大物母材や厚盛が可能、又現地工事も可能。
-
プラズマ溶射
プラズマ溶射は、溶射ガン内部に対向して置かれた陰極と陽極の間に電圧をかけて直流アークを発生させ、アークによって、作動ガスを電離させて高温の熱プラズマを作ります。
プラズマにより、ガスを急速に膨張させ、高温・高速のジェットとしてプラズマフレームが形成されます。特徴
- 極めて高温(10,000℃以上)である為、高融点のセラミックも溶射可能です。
- 溶解せずに分解や気化するような物質を除けば、どのような材料でも溶射可能です。
- 被膜は高密度で、基材との密着性が良好。